I did a little experiment today. I took one of my photos (sunrise over the Gulf of Mexico on New Years Day 2025) and stretched it to be twice as wide as it was originally. Here is the result. Not bad, eh? I used the Seamcarve filter in the G’Mic-Qt plugin for GIMP. Here is […]
Recent Posts
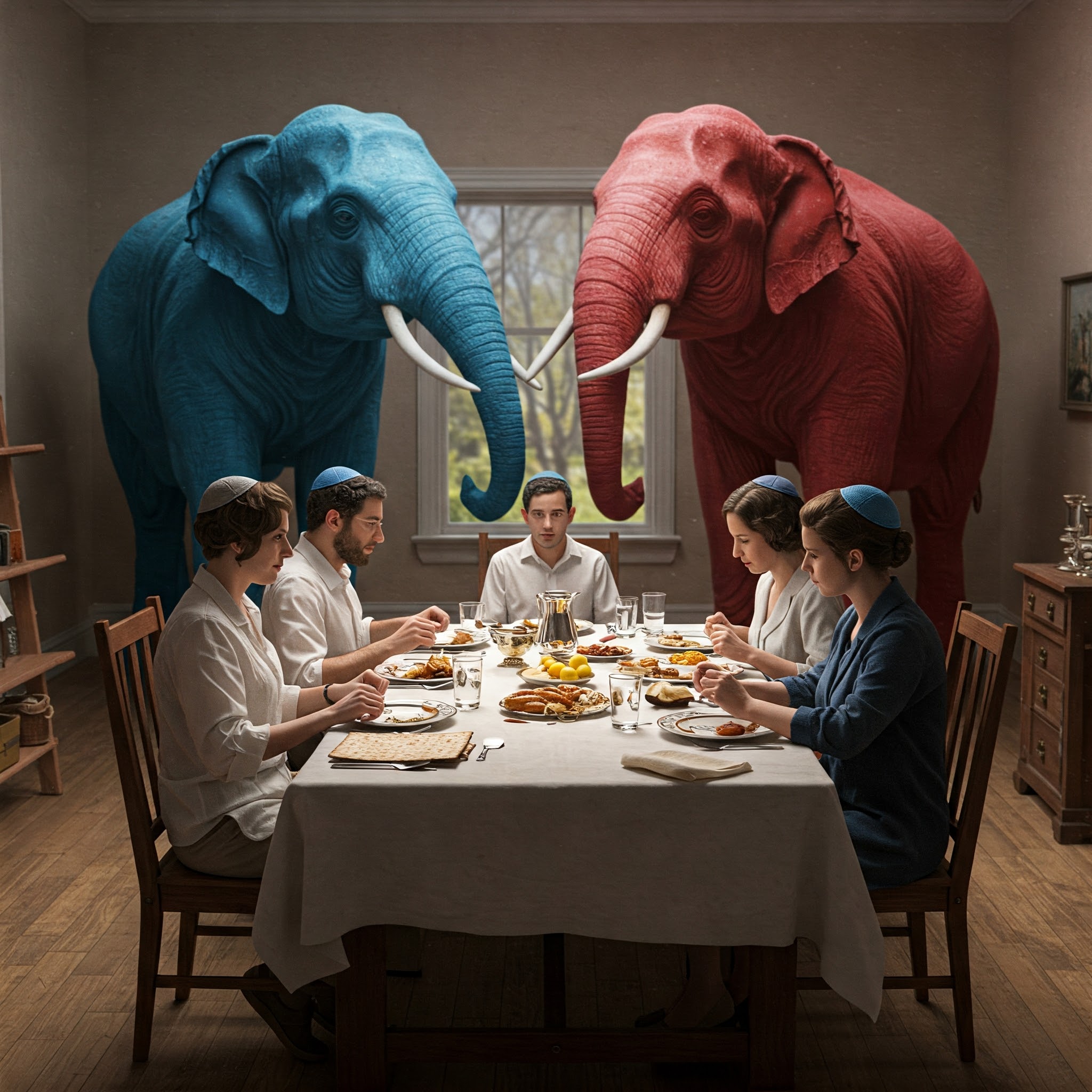
There are Elephants in the Room
There are elephants in the room that would like some attention and it’s time we give it to them, because it might literally be a matter of life and death. These elephants have been around as long as people, but they’ve gotten a lot meaner and scarier since last Passover.
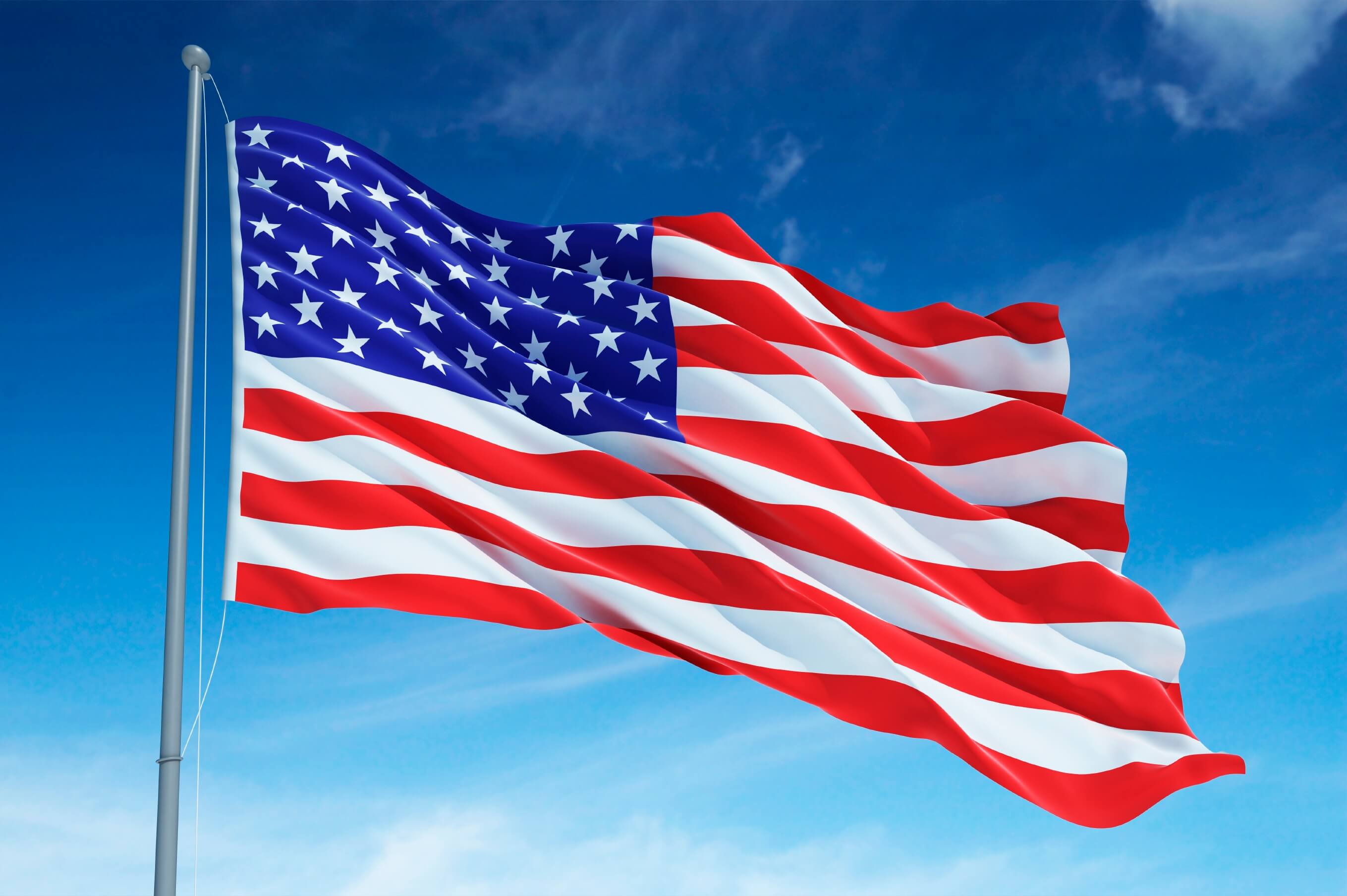
Let’s Eliminate Real WFA
I received an email today from a museum that I care deeply about, the St. Louis Kaplan Feldman Holocaust Museum. Some of its funding is threatened since the federal Institute of Museum and Library Services (IMLS) has been effectively shut down. When I investigated further, I discovered that IMLS also supports many other Missouri organizations […]
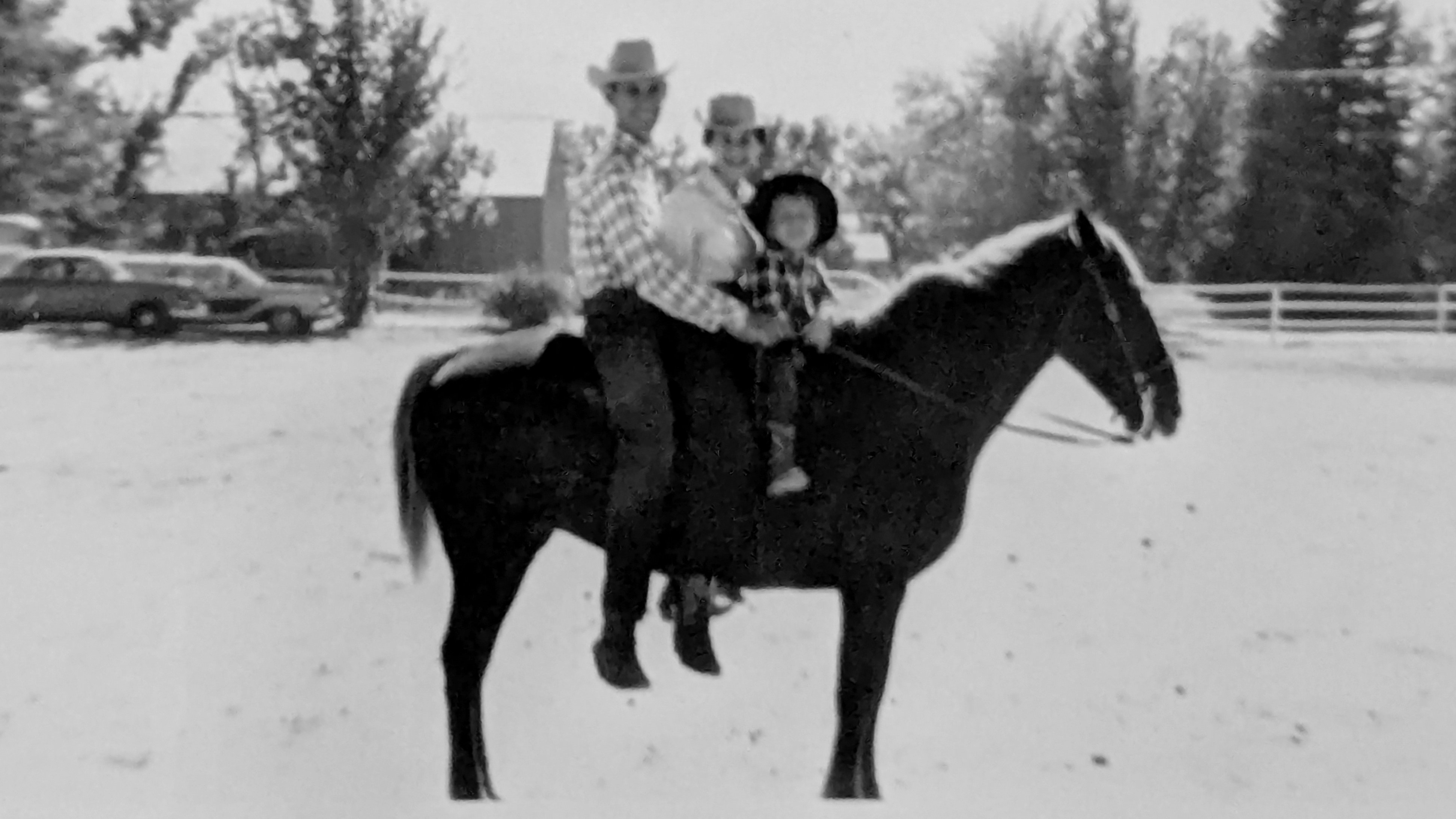
Thumb Wrist Neck Waist Height
I was somewhat older than I am in this photo of my parents and me when my dad taught me something kind of amazing. It popped into my brain while I was trying to take a nap this afternoon. Go get a long piece of string or yarn. Wrap it around your thumb. Now double […]
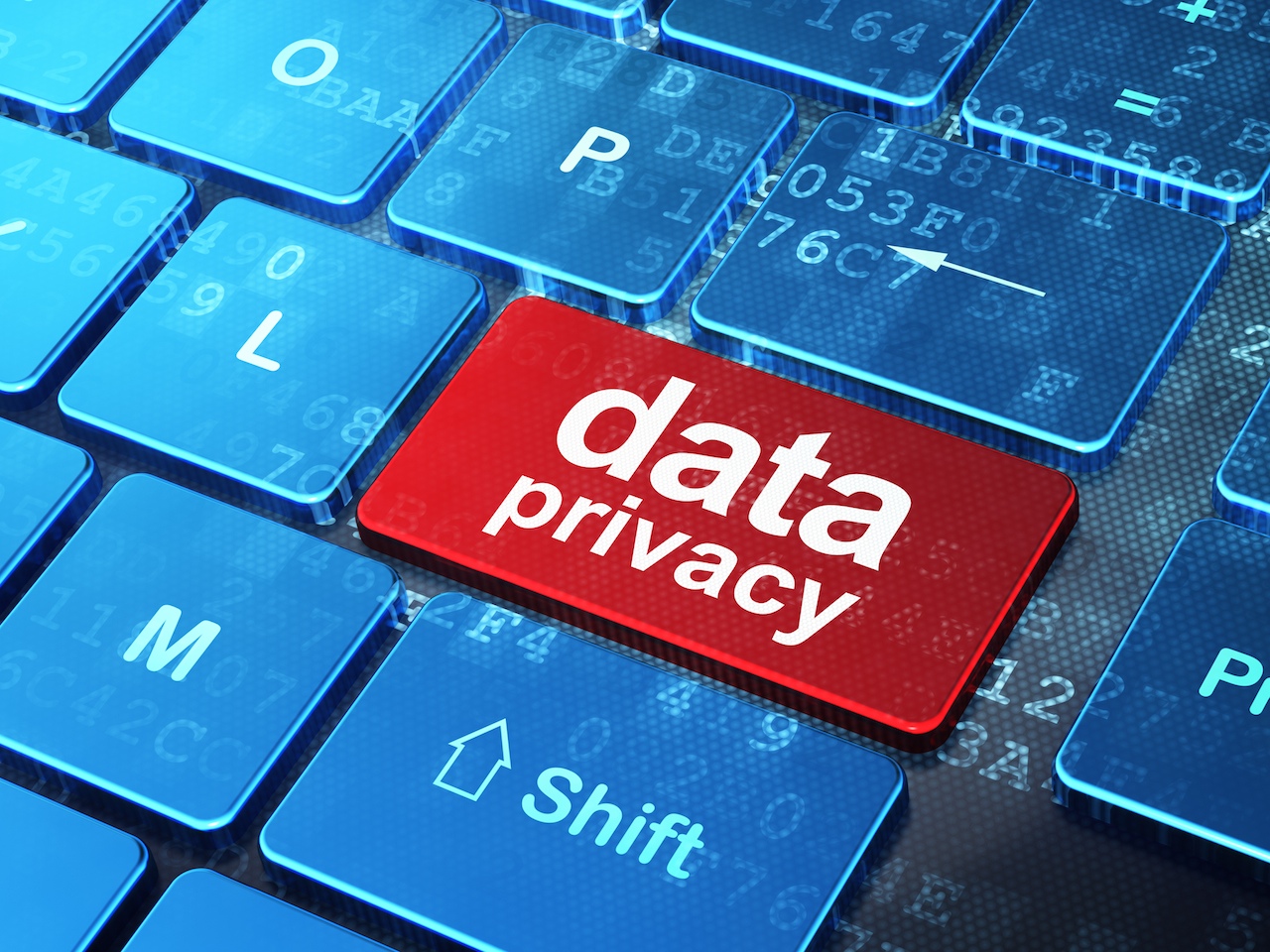
Avoid Targeted Advertisements
I would wager that you have been dismayed to see an advertisement targeting you very shortly after you searched for similar products. Maybe the ads showed up in Facebook. Maybe they showed up on a completely unrelated website. This practice goes by several names: targeted advertising, targeted marketing, and remarketing to name a few. It […]
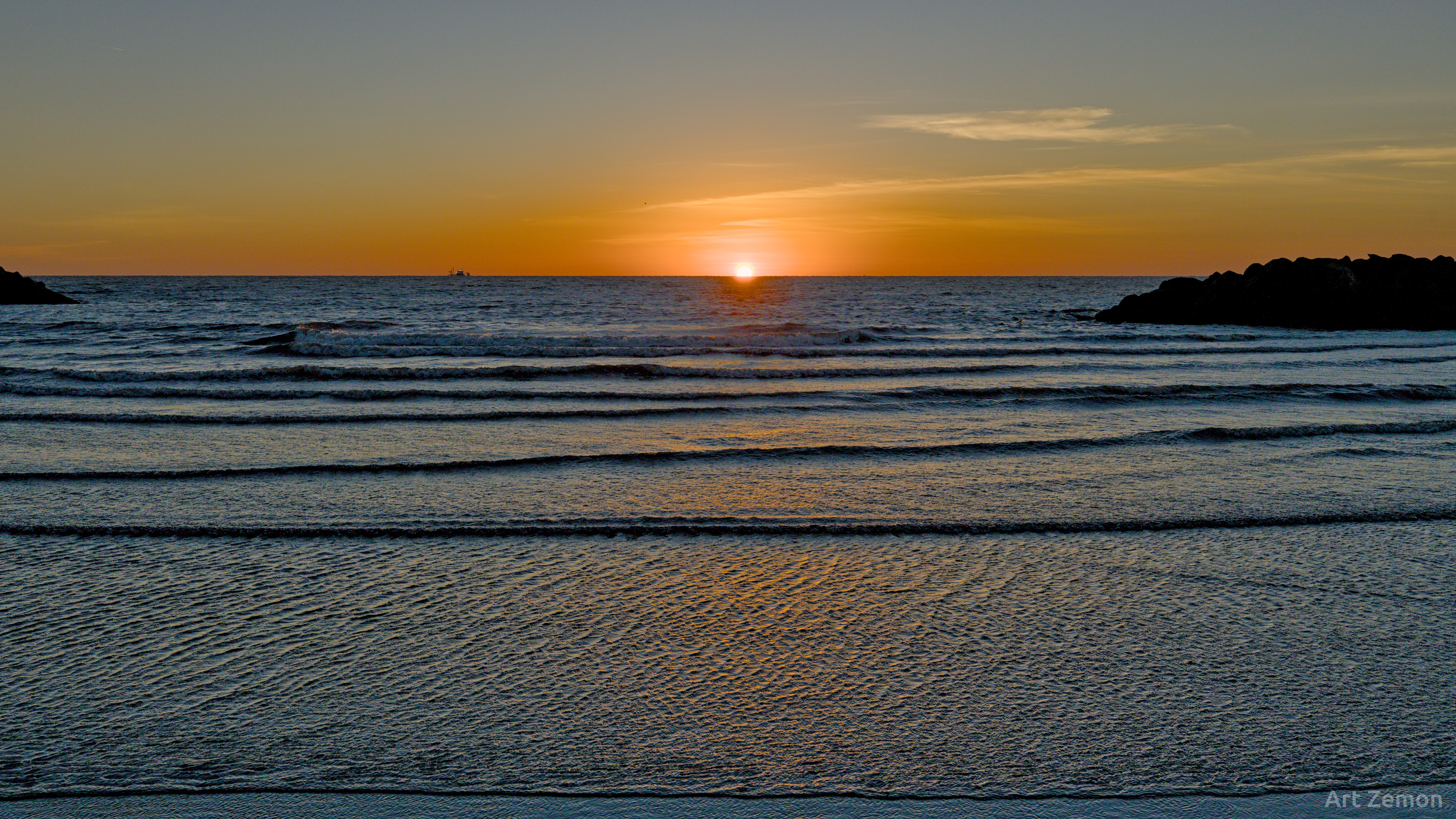
Sunrise over the Gulf of Mexico
Back in December, I decided that I wanted to start 2025 by watching the sunrise over the Gulf of Mexico from Grand Isle, LA. Candy and I hauled our travel trailer down to Grand Isle State Park. The weather cooperated, and I got three gorgeous shots. Here are small versions of the photos that I […]
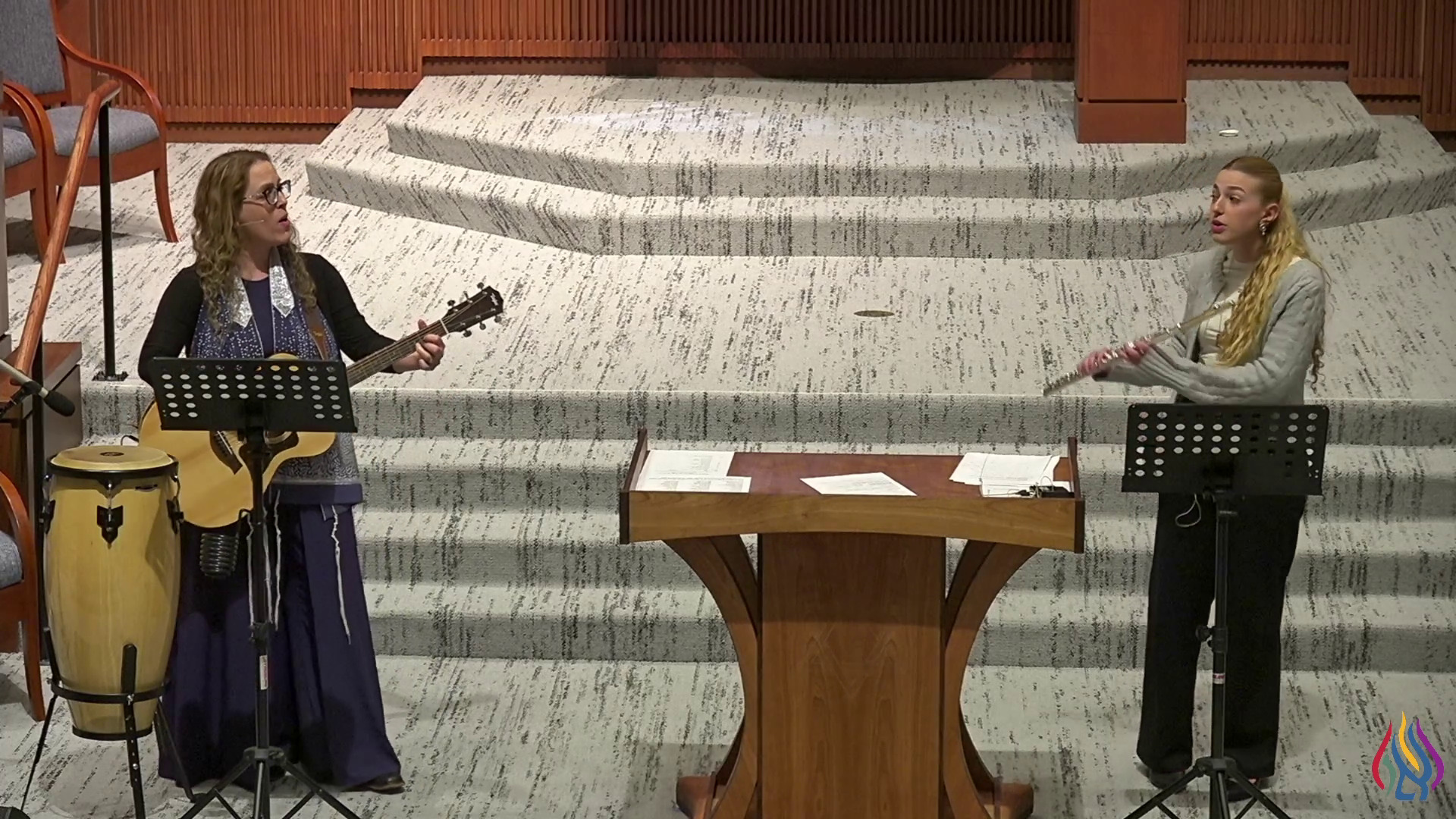
Come Back – תחזור
I want to share a beautiful song with you, Come Back performed here by two Israelis, Cantor Shirel Richman and Shinshinit Gaya Zohar. Earlier this week, Hamas released three civilian Israeli hostages, all young women, in exchange for 90 convicted Palestinian prisoners. Today, Hamas released four Israeli soldiers, all women ages 19 and 20, in […]
More Recent Posts
- Come Back – תחזור
- Warm Weather Pictures for a Grey Day
- My Hands Shook with Essential Tremor
- Centr Multi-Gym Review
- Springfield and the Quad Cities
- Launching into an RV Life
- STL2ATL 14-16 – Chattanooga, TN to Marietta, GA
- STL2ATL Day 13 – a Long Long Day from Winchester, TN to Chattanooga, TN
- STL2ATL Days 10-12 – Nashville, TN to Tims Ford State Park
- STL2ATL Days 6-9