I started on the firewall for my Bede BD-4C airplane tonight. Being a fire wall, it is stainless steel instead of aluminum. It is also surprisingly thin, just 26 gauge, about .019 inches.
I needed to make rectangular cutouts in each corner to allow for the engine mounts. Drilling the pilot holes for the corners of these cutouts showed me just how easy I have had it working with aluminum up until now. When I drill aluminum, it is basically the same as drilling wood. The bit goes right through. This stainless steel is a whole different animal. Even using a pretty new #40 bit, it still took quite a bit of drilling and pressure to penetrate the metal. And when the bit hit the wooden block behind the steel, a little whiff of smoke curled up. Hot stuff!
Here is what I have so far.
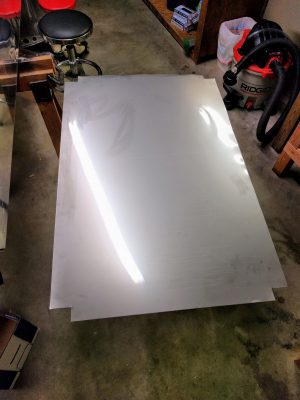
Now the fun begins. The firewall goes onto the front of the fuselage, which looks like this:
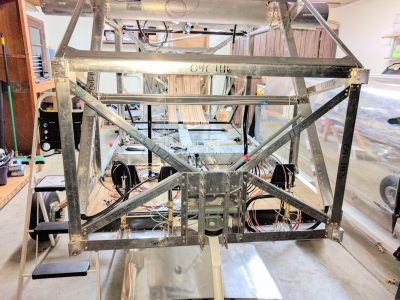
Yup… you’re right. The firewall goes underneath every single one of those bolts. But the real fun is that I cannot just pull all of the bolts and clecos out at the same time because they are holding the fuselage together. Instead, I will do this:
- Remove a few bolts.
- Hold the firewall in place and back drill the steel through the existing bolt holes.
- Reinstall the bolts, attaching the firewall to the fuselage.
- Repeat until done.
If you have ever wanted to drill holes in stainless steel, I have a golden, er silver-ish opportunity for you. C’mon over!
Drilling the firewall should be fairly easy with a sharp bit. Go slow, press hard (always keep cutting, not just rubbing), and add cutting oil. There should be no smoke. What are you planning to use to feed wires and such through the FW?