When I started cutting up steel for the back seat frame of my Bede BD-4C airplane, the chop saw threw off so many sparks that I singed the top of my wooden workbench. Being a bright boy, I thought that moving the saw to a metal table would be just a wee bit safer. 🙂
I went shopping and found the cheapest possible welding table at (no surprise) Harbor Freight. $79 seemed like too much money for a crappy tool, though, so I decided to build a welding table. It would be fun (I love flame!) and educational (I would learn more about welding) and less expensive (I’m cheap). I found a set of welding table plans at Lincoln Electric to use as a guide.
I visited Shapiro Metal Supply and was delighted with the experience. I must have been a sight, driving into a metal recycling business in a bright yellow Fiat 500, but the folks at Shapiro still treated me well and got me what I needed right quick. I walked out with 84 pounds of steel for just $55, plenty of metal to make a welding table and have a bunch of scrap left over just for practicing welding.
Last night, I spent about three hours mitering the ends of four pieces of steel angle, welding up the frame for the table top, and then welding on a sheet of 1/8 inch plate. My table top is done and here are the pictures to prove it.
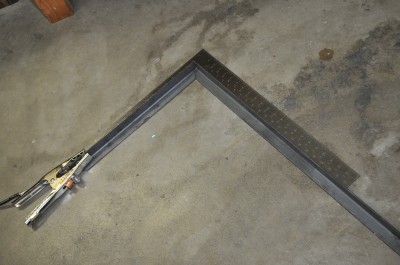

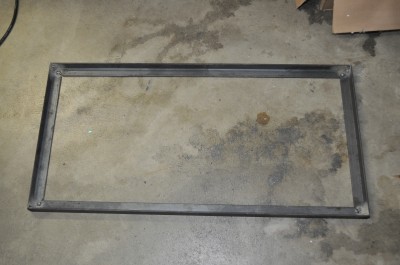

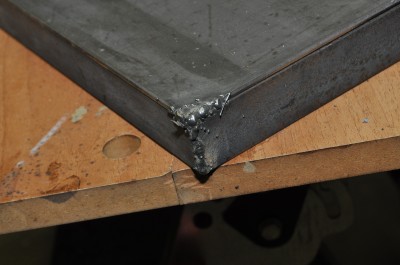
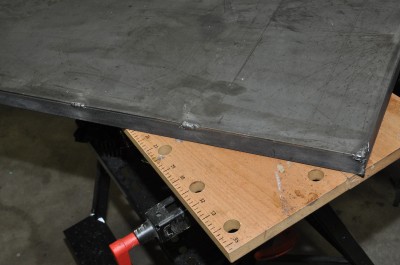
I am definitely learning. Switching from trying weld with solid wire (MIG wire) without shielding gas to using flux wire (flux welding) took care of the initial problems that I was having. Now the problem is lack of skill but I’m working on that one. As I build the rest of the pieces of my table, I will trying a lower wire feed rate. Please post a comment below if you have other suggestions.
Wish I had known before Bets and I visited a few weeks ago. Would have also packed my 2 1/2 X 5′ welding table for you to use for the duration. It may seem large but it stands on end when not in service. When in storage mode it rolls about easily on casters. What else do you need that I may have and can save you some money on? ‘gnore the English, I’m not taking the time to fix it.
Pete
Although you are indeed a terrible welder and have god awful taste in automobile colors, I enjoyed this post and like your sense of humor. Hopefully the more you get into welding the better you’ll become….as for your choice in yellow transportation….tastes can change, right
Sorry, didn’t read the post completely. Forget the flux – Mig with gas is where you need to be headed if your serious.
Thanks for the tip. I think you’re probably right about switching from flux to MIG. And… real men can drive yellow cars. 🙂
Art, glad you handled the ribbing on the car with a smile…… Just going to give you a tip. It boils down to three things heat, wire speed, and lateral speed. As a young man I learned from my uncle, a certified welder, who gave me the basics. Putting on a mask and watching someone who – actually does know – what they are doing can help tremendously. If that’s not really an option, you can find anything on youtube. Also, most welders will have a chart for wire speed and heat for a given steel thickness, this will give you at least a starting point. From there on “practice makes perfect”, as they say.