As promised, here are photos of the intricate woodwork in the otherwise aluminum Bede BD-4C. 🙂 There is a 7′ long aluminum tube which runs through the fuselage to activate the horizontal stabilator. The ends of this push-pull tube have aluminum clad hardwood inserted into them.
I cut the wood roughly to shape. The .063″ thick aluminum gets bonded to the wood with 3M Scotch-Weld 2216 epoxy and bolted in place. Once I get the epoxy and glue the aluminum to the wood, I will do the final sanding so that everything is neat and tidy.
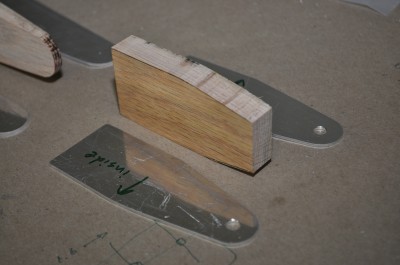
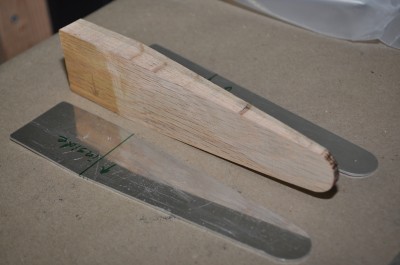
It might be a little hard to imagine how these get used from pictures of partly assembled parts and my words so here is a picture of the front of the tube “attached” to the pivot arm.
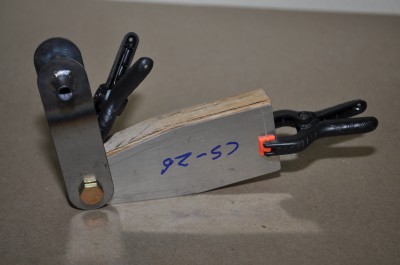
Here is a photo of the back end of the tube “attached” to the bottom half of the bracket which holds the spar for the horizontal stabilator.
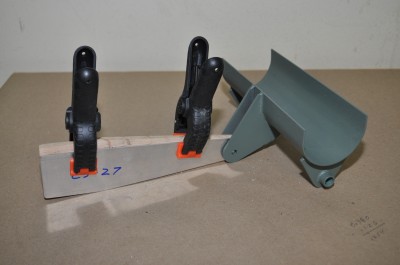
After doing all this complex woodwork, I missed making brackets so I made a couple more. (Are you tired of reading about brackets, yet?)
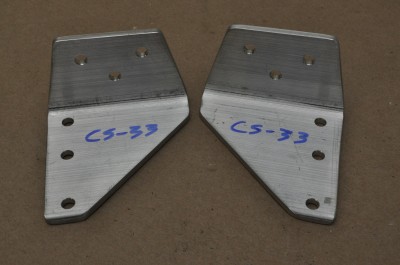
These latest brackets are .125″ thick 6061 aluminum (stronger than the 2024 aluminum used for most of the rest of the parts). They go at the wing roots and hold part of the controls for the ailerons.
What I see is extreme detail and patience.
That’s some well furnished workshop you’ll have when all is done, besides the flying machine.
Thinking
on building one. Could we talk.
Don: I emailed you directly. I’d love to talk to you about building a BD-4C. Reply to my email or call me. — Art Z.